
Refrigerant
With a GWP value of 1774, R407C exceeds the regulatory thresholds for environmentally friendly refrigerants. In the long term, it will no longer meet the requirements of the regulation.
Continued Operation and Maintenance of Existing Systems
Existing systems using R407C can continue to operate.
The regulation primarily targets new installations. However, the following aspects may become relevant in the future:
- Maintenance and Repairs: Work on the refrigeration circuit will remain permissible as long as the refrigerant is available.
- Refilling with R407C: Availability of R407C may decrease over time due to its high GWP value and the gradual phase-down of fluorinated gases, potentially leading to higher prices.
New Regulations Effective from 2025
From January 1, 2025, stricter requirements will apply to certain systems. Monosplit systems with a refrigerant charge of less than 3 kg will no longer be allowed to use refrigerants with a GWP value above 750. This includes refrigerants like R410A and R407C, which will no longer be permitted in such systems.
Recommendations for System Operators
Operators should conduct regular maintenance to prevent leaks and ensure system efficiency. For repairs or new installations, it is crucial to consider current regulations and anticipate future developments. Transitioning to natural refrigerants such as CO₂, propane, or ammonia is a viable alternative, as these options comply with legal requirements and often provide greater energy efficiency.
Economic Feasibility and Future Developments
The use of R407C may become increasingly expensive and challenging in the coming years. The availability of this refrigerant is expected to decline as the allowable market volume of fluorinated refrigerants is gradually reduced. This may also lead to rising prices for R407C. In cases of significant repairs or leaks, an early transition to climate-friendly alternatives could prove economically advantageous.
Conclusion
R407C can continue to be used in existing systems, provided they remain in good technical condition and are regularly maintained. However, operators should consider transitioning to more environmentally friendly alternatives such as natural refrigerants in the long term. These not only meet future legal requirements but also offer potential economic benefits and improved energy efficiency.
R513A is a low Global Warming Potential (GWP) hydrofluoroolefin (HFO) refrigerant blend developed as a transitional replacement for R134a in various refrigeration applications. With a GWP of 631, R513A offers a significant reduction in environmental impact compared to traditional refrigerants, making it an attractive option for new systems as well as retrofitting existing ones.
Applications
R513A is suitable for use in:
- Commercial refrigeration
- Industrial refrigeration
- Medium-temperature direct expansion systems
- Chillers and heat pumps
Advantages
- Low GWP: With a GWP of 631, R513A provides a 56% reduction in global warming potential compared to R134a.
- Energy efficiency: It closely matches the performance characteristics of R134a, allowing for energy savings without compromising efficiency.
- Safety: Classified as A1, R513A is non-flammable and poses minimal risk during handling and use.
- Compatibility: It can be used in existing R134a systems with minor modifications, making it a practical retrofit option.
Technical Data
- ASHRAE Number: R-513A
- Composition (wt%):
- R1234yf: 44%
- R134a: 56%
- Molecular Weight: 76.0 g/mol
- Boiling Point at 1 atm (101.3 kPa): -47.0 °C
- Critical Temperature: 74.9 °C
- Critical Pressure: 4,000 kPa (abs)
- Ozone Depletion Potential (ODP): 0
- Liquid Density at 21.1 °C: 1,200 kg/m³
- Temperature Glide: Minimal
Regulatory Status
As a refrigerant with a GWP below the threshold set by the F-Gas Regulation, R513A is classified as a transitional refrigerant. This means it is currently allowed for use but is subject to future regulations aimed at reducing the overall environmental impact of refrigerants.In summary, R513A represents a viable solution for industries looking to reduce their carbon footprint while maintaining system performance and safety standards. Its compatibility with existing systems and lower environmental impact make it an essential option in the transition towards more sustainable refrigerants.
The refrigerant R410A, with a GWP (Global Warming Potential) of 2,088, is being gradually restricted and eventually banned in the European Union. Below are the key dates and restrictions:
Bans for New Installations
- From January 1, 2025: Ban on plug-in room air conditioners, monoblock air conditioners, and other self-contained air conditioning systems and heat pumps with a capacity of up to 12 kW.
- From January 1, 2027: Ban on chillers with a capacity above 12 kW.
- From January 1, 2029: Ban on split systems with a capacity up to 12 kW.
Restrictions for Existing Systems
- From January 1, 2026: Ban on the use of virgin refrigerants with a GWP above 2,500 for air conditioners and heat pumps.
- From January 1, 2032: Ban on the use of virgin refrigerants with a GWP above 750 for air conditioners and heat pumps (with the exception of chillers).
Use of Recycled R410A
- Until December 31, 2031: Processed and recycled refrigerants with a GWP above 2,500 (such as R410A) may still be used.
- From January 1, 2032: Recycled R410A may only be used under certain conditions:
- It must be used by the company that performed the recovery during maintenance or servicing.
- Alternatively, it may be used by the company for which the recovery was performed during maintenance or servicing.
It is important to note that these regulations are part of the new F-Gas Regulation (EU) 2024/573, which came into force on March 11, 2024.
The goal of this regulation is to phase out climate-damaging partially halogenated fluorocarbons (HFCs) by 2050.
Alternatives to R134a
In automotive air conditioning systems with open compressors and hose connections in the refrigeration circuit, the risk of leakage is significantly higher than in stationary systems. To reduce direct emissions in this area of application, the EU issued Directive 2006/40/EC. Since 2011, this directive mandates that only refrigerants with a GWP < 150 are approved for type certification of new vehicles. Consequently, the previously used R134a (GWP = 1430) is no longer permitted in these systems.
Alternative refrigerants and new technologies have since been developed and tested. In this context, the use of R152a was also closely examined. However, the automotive industry has now agreed on system solutions with so-called "low GWP" refrigerants, which will be discussed below.
R152a – An Alternative to R134a (?)
R152a is very similar to R134a in terms of volumetric cooling capacity (-5%), pressure levels (-10%), and energy efficiency. It even offers favorable properties such as reduced mass flow, vapor density, and associated pressure drop (-40%). R152a has been used for many years as a component in blends but has not yet been applied as a single-component refrigerant. Its exceptionally low global warming potential (GWP = 124) is a notable advantage.
However, R152a is flammable due to its low fluorine content and is classified in Safety Group A2. This imposes higher safety requirements, necessitating tailored design solutions, safeguards, and corresponding risk analyses. For this reason, the use of R152a in vehicle air conditioning systems is considered unlikely.
"Low GWP" HFO Refrigerants R1234yf and R1234ze(E)
The ban on R134a in vehicle air conditioning systems within the EU has triggered several research projects. In addition to CO2 technology (see page 35), refrigerants with very low GWP values and thermodynamic properties similar to R134a have been developed.
In early 2006, two refrigerant blends, "Blend H" (Honeywell) and "DP-1" (DuPont), were introduced. INEOS Fluor followed with a variant under the trade name AC-1. These refrigerants were essentially blends of various fluorinated molecules.
During the development and testing phases, it became apparent that not all acceptance criteria were met, leading to the discontinuation of further investigations with these blends.
DuPont (now Chemours) and Honeywell subsequently formed a joint venture focusing on 2,3,3,3-Tetrafluoropropene (CF3CF=CH2), marketed as R1234yf, a member of the Hydrofluoroolefin (HFO) group. These unsaturated HFCs feature a chemical double bond.
R1234yf has an extraordinarily low GWP (GWP100 = 4). Upon release into the atmosphere, the molecule breaks down rapidly within days, resulting in a very low GWP. However, this raises concerns about its long-term stability in the refrigeration circuit under real-world conditions. Extensive testing has demonstrated the required stability for automotive air conditioning systems.
It has been determined that the increased risk of flammability associated with R1234yf can be mitigated through appropriate design measures. However, studies (e.g., by Daimler-Benz) have identified elevated risks, prompting some manufacturers to intensify the development of alternative technologies.
Toxicity tests have shown very positive results, as have compatibility tests with plastics and elastomers commonly used in refrigeration circuits. Lubricants, however, show increased chemical reactivity in some cases, which can be addressed with appropriate formulations and stabilizers.
Field and laboratory testing experiences have been positive, particularly regarding performance and efficiency. Cooling capacity and COP are within 5% of R134a in typical automotive air conditioning applications. With proper system adjustments, similar performance and efficiency to R134a can be achieved.
Critical temperature and pressure levels are also similar, while vapor density and mass flow are approximately 20% higher. Discharge gas temperature is up to 10K lower.
Due to the relatively straightforward adaptation of automotive air conditioning systems, this technology has prevailed over competing CO2 systems. However, due to the flammability of R1234yf, other technical solutions are gaining attention, such as active extinguishing systems (e.g., using argon) and further developments in CO2 systems.
Other Applications for HFO Refrigerants
The use of R1234yf in other mobile air conditioning applications is under consideration, as is its use in stationary air conditioning and heat pump systems. However, A2L refrigerant charge limits (e.g., EN378) impose restrictions on these applications. Questions about long-term stability in refrigeration circuits with typically long service lives must also be addressed.
For applications requiring A1 safety group refrigerants (neither flammable nor toxic), alternative R134a refrigerants with lower GWPs based on HFO/HFC blends have been developed and are already in use.
R1234yf and R1234ze(E), described below, are also used as base components in HFO/HFC blends. These blends were developed to comply with legal regulations, such as the EU F-Gas Regulation, as "low GWP" alternatives to R134a, R404A/R507A, R22/R407C, and R410A. Some of these refrigerants have been tested in the AHRI Alternative Refrigerants Evaluation Program (AREP) and are in practical use.
Another Hydrofluoroolefin, R1234ze(E), primarily used as a propellant in PU foams and aerosols, is now available. It differs from R1234yf in molecular structure. Its thermodynamic properties make it suitable as a refrigerant, with a similarly low GWP (GWP100 = 7).
Uncertainty often arises regarding flammability. R1234ze(E) is classified as non-flammable for transport and storage but is flammable at the 60°C test reference temperature used for refrigerants. It is thus classified in Safety Group A2L, like R1234yf.
R1234ze(E) is sometimes referred to as an R134a substitute but has more than 20% lower volumetric cooling capacity and a boiling point (-19°C) that limits its use at low evaporation temperatures. It is primarily used in chillers and high-temperature applications.
For more information, see page 36, "Special Applications."
Courtesy of Bitzer Kühlmaschinenbau GmbH
Source: Bitzer Refrigerant Report 19
INTRODUCTION
Refrigerant is essential as an operating fluid for heat transport in refrigeration systems, air conditioning systems and heat pumps. There are different types of refrigerants with different environmental impacts should they be released into the atmosphere.
We explain which refrigerants you are allowed to use and which refrigerants are no longer allowed according to regulations.
Refrigerant types
There are different types of refrigerants that have been used over time. In the past, greenhouse gases (HCFCs) containing chlorine, such as R-12 or R-22 (chlorodifluoromethane), were often used as refrigerants. These have been replaced by chlorine-free refrigerants, such as R404A, R-134a or R-32, due to their harmful effects on the ozone layer.
Natural refrigerants such as propane, butane, isobutane, CO2 or ammonia have a better environmental balance compared to synthetically produced ones. Even water can be used as a refrigerant and is the most environmentally friendly of all.
Damage to the ozone layer
Older chlorinated refrigerants (HCFCs) contribute to the destruction of the ozone layer, leading to an increase in UV radiation on the Earth's surface. The Montreal Protocol provides for the gradual phase-out of these ozone-depleting refrigerants. What is unique about this protocol is that it was ratified by all 187 UN member states in 1988.
Currently, 193 member states are counted.
Several amendments to the protocol have tightened the regulations, most recently the decision in Kigali in 2016. Partially fluorinated substances (HFCs) are included in the Montreal Protocol and regulate the gradual restriction of the consumption of such refrigerants.
The global warming effect
Besides the depletion of the ozone layer, there is another known problem with refrigerants.
These can make a significant contribution to increasing the greenhouse effect in the atmosphere. When refrigerants enter the atmosphere, heat radiation from the sun is absorbed. This contributes to global warming.
Therefore, the Global Warming Potential (GWP) is an important factor in assessing the environmental impact of a refrigerant.
The F-Gases Regulation and the Montreal Protocol regulate the phasing out of refrigerants with a high GWP value.
Manufacturers are working hard to develop alternative refrigerants with a low GWP value.
The difficult thing is that the "old" refrigerants have a high safety class, which is more difficult to comply with if the GWP value is minimised.
Roughly speaking, the lower the GWP value, the greater the flammability.
The more flammable a refrigerant is, the lower its safety class.
The lower the safety class, the higher the technical requirements for operating systems with such refrigerants.
Environmentally friendly alternatives are sought
Modern refrigeration and air conditioning systems are increasingly using more environmentally friendly refrigerants with lower GWP.
For example, R-410A, a commonly used refrigerant in air conditioning systems, has no ozone depleting potential (ODP value), but it has a high GWP value of 2088. Other refrigerants such as: R-32 have a lower GWP value of 675 and are currently considered a more environmentally friendly alternative.
In the F-Gas Regulation, the phase-down process for all member states regulates the phasing out of refrigerants by 2030, which refrigerants are no longer allowed at which point in time and how long existing systems may be operated. Additional findings from current research can accelerate the phase-down process.
For example, it should be clarified by October 2023 how fluorinated carbon chains, in which the hydrogen atoms are completely or partially replaced by fluorine atoms, are to be handled. This will primarily affect the refrigerants of the R-400 and R-100 series.
According to current knowledge, the so-called PFAS are carcinogenic and difficult to break down in the human body.
PFASs are widespread in various industries and applications.
This does not only apply to refrigerants in refrigeration and air conditioning systems, but also to the air conditioning industry:
- Coatings for textiles
- Outdoor clothing
- Impregnations
- Baking paper
- Fire extinguishers
- Cosmetics
- etc.
Leaks and maintenance
Refrigerant can be released into the atmosphere due to leaks in the system or improper maintenance. Proper handling of the refrigeration and air-conditioning systems, as well as regular leakage tests, are important in order to eliminate or minimise environmental pollution.
The use of detachable screw connections in refrigerant pipelines should be avoided. Where technically possible, fixed connections should be made by welding or soldering in the pipe network.
Depending on the filling quantity of the system or the CO2 equivalent of the refrigerant, system documentation is mandatory.
Disposal
When replacing or disposing of refrigeration and air conditioning equipment, local environmental regulations and disposal guidelines for the refrigerant contained therein must be followed. Refrigerant must be recovered from the refrigerant circuit and properly disposed of or recycled.
Conclusion
It is important to use environmentally friendly refrigerants in refrigeration and air conditioning systems to reduce environmental impact.
If it is technically possible, if the application allows it, natural refrigerants are the most likely to be used.
Care and maintenance of refrigeration and air conditioning systems is essential. It should be carried out by specialists or by persons who have the necessary know-how, tools and are informed about and certified in the latest environmentally friendly technologies.
If you notice any defects, report them to your service partner as soon as possible.
Regular maintenance of the equipment is the be-all and end-all. Not only for the environment, but it also saves you money.
History of Ammonia in the Refrigeration Industry
Ammonia (NH₃ or R717) is the refrigerant that was first used in vapor compression machines around 1870. It has thus been used in large-scale refrigeration and industrial systems for more than 100 years.
Key Data
NH₃ has the lowest TEWI (Total Equivalent Warming Impact = direct greenhouse effect of the refrigerant as well as indirect greenhouse effect due to the energy consumption of the system).
The ozone depletion potential (ODP) of ammonia is 0, making it relatively environmentally friendly.
Due to the low molar mass of NH₃ compared to air, gaseous refrigerant escaping from a refrigeration system rises quickly in the room and can be vented out through a fan near the ceiling.
In the stratosphere, the lifetime of NH₃ is about seven to fourteen days, classifying it as a short-lived substance.
The evaporation temperature of NH₃ is approximately -33°C (at atmospheric pressure).
Refrigeration systems with an evaporation temperature lower than -33°C operate in a vacuum. As a result, any leaks on the suction side will allow air and moisture to enter the refrigeration system.
NH₃ has a strong affinity for water (moisture entry). One kilogram of water can theoretically dissolve up to 7 kilograms of NH₃, resulting in ammonium hydroxide (ammonia water). Dissolving NH₃ is an exothermic process, which heats the solution significantly.
An NH₃ system with high water content experiences a loss in performance. In such cases, it is recommended to install an NH₃ drying system (even on loan).
Systems operating in a vacuum should generally be equipped with an automatic air purger to continuously remove non-condensable gases from the refrigeration system.
Another important point in NH₃ refrigeration systems is the compressor oil.
Unlike freons, NH₃ does not mix with standard oils, resulting in a fundamentally different oil return process.
Furthermore, NH₃ systems must be made of steel or stainless steel because NH₃ attacks and destroys copper and, for example, bronze. As a result, manufacturers and products for NH₃ refrigeration systems are often different from those for conventional freon or CO₂ refrigeration systems.
But:
In the conventional refrigeration industry, NH₃ has a reputation for being dangerous! Is this a prejudice?
In my opinion, this fear is completely unfounded!
How dangerous is NH₃?
In the past, ammonia smelling salts were used to revive unconscious people. Today, it is used, for example, to treat patients with borderline personality disorder.
While countless people around the world collect their breakfast eggs from chicken coops without being deterred by the strong ammonia smell, NH₃ is considered a health risk in industrial machine rooms.
In fact, NH₃ is comparatively less dangerous than CO₂.
The human detection threshold for NH₃ is 1–3 ppm, which is so low that people would flee long before a harmful concentration is reached.
CO₂, on the other hand, has no odor. It is heavier than air, settles in the lungs upon inhalation, and cannot be coughed out. Suffocation is almost inevitable.
In newly built NH₃ refrigeration systems, you can hardly smell anything!
NH₃ refrigeration systems are subject to high safety requirements set by current standards and regulations, making an emergency scenario nearly impossible.
Only during system filling or maintenance can a small amount of toxic ammonia escape. A trained refrigeration technician protects themselves through deliberate, practiced procedures and personal protective equipment (PPE).
It is important to remember that NH₃ is flammable. It ignites at concentrations between 15% and 28% in air.
However, the complete shutdown of a system occurs at a concentration of approximately 30,000 ppm, or about 3%.
The ignition temperature of NH₃ is very high at 650°C, and combustion must be maintained by an external flame.
Nevertheless, high concentrations of NH₃ in enclosed spaces must be avoided! This is achieved by installing a ventilation system in accordance with regulations and standards. As a result, the risk of a fire can be almost entirely eliminated when operating an NH₃ system with care.
Cost Check
In terms of total costs, NH₃ refrigeration systems perform particularly well compared to R134a and R404A, due to their low operating costs.
Even in comparison to the now-banned refrigerant R22, NH₃ is clearly superior, primarily due to its low energy consumption.
With NH₃’s exceptionally high enthalpy difference (approximately six times higher than R22) and relatively low circulating mass flow, NH₃ achieves by far the best values.
This means that NH₃ provides the highest cooling capacity per kilogram of refrigerant.
Thus, NH₃ refrigeration systems achieve high COP values (Coefficient of Performance) compared to other refrigerants.
Additionally, NH₃ is by far the most cost-effective refrigerant compared to all others.
Conclusion
From an economic perspective and in terms of environmental friendliness, NH₃ is the ideal refrigerant.
Its toxicity should not be a deterrent, as, after all, sniffing a bit of NH₃ clears the sinuses.
R. Desens
In addition to environmental friendliness, hydrocarbons offer cost advantages in heating / cooling and freezing. As a common substitute for hydrofluorocarbons (now considered to be harmful to the environment), HCs can handle the oils and other components found in many existing systems. In addition, they are inexpensive and result in a significantly better energy efficiency, which is reflected in lower operating costs.
A hydrocarbon (HC) is a chemical compound between hydrogen and carbon. These elements occur in nature, such as in high concentration in crude oil. As innovative, non-toxic refrigerants, hydrocarbons are an environmentally friendly alternative to ozone-depleting fluorocarbons (CFC / HCFC / HFC).
HCs are flammable, but the use of propane (R290) for cooking and heating is common practice. Certain rules for the safe use of such materials are necessary and accepted by all users.
Several HC types can be used as refrigerants, but isobutane (R600a) is the most commonly used HC in household refrigerators and freezers. Propane (R290) is used more in commercial heat pumps, air conditioners, and refrigerators and freezers.
History of the refrigerants
Important data
- China, January 2030 - 60% reduction in HFC emissions (previously no specific regulations known)
- China, January 2025 - 25% reduction in HFC emissions (no specific regulations known so far)
- Europe, January 2022 - HFC ban with GWP> 150 in commercial refrigerators and freezers
- USA, January 2021 - Ban on R134a in air conditioning systems of vehicles
- USA, January 2020 - HFC ban in all MBP applications & standalone LBP systems
- Europe, in January 2020 - HFC ban with GWP> 150 in-air air conditioning systems
- Europe, January 2020 - HFC ban with GWP> 2500 in commercial refrigerators and freezers
- USA, January 2019 - HFC ban in vending machines and all "MBP" refrigeration systems (<2200 BTU / h)
- USA, January 2017 - Ban on HFCs in supermarket systems
- USA, July 2016 - HFC ban in all retrofit refrigeration systems
- Europe, January 2015 - Limitation of HFC quantities for import and production (+ tax increases)
- Europe, January 2015 - HFC ban with GWP> 150 in household refrigerators and freezers
- Worldwide January 2015 - Complete ban on R12 and start of phase-out phase R22
Hydrocarbons and the environment
HC refrigerants are not considered an ozone layer destroyer, and most species have a global warming potential (GWP) of magnitude 3. By comparison, the synthetic refrigerant R404A (for which HCs are a common substitute today) has been astronomical high GWP of 3260.
Systems with HC refrigerants play a dual role in reducing levels of harmful greenhouse gases. Firstly, the direct emissions of greenhouse gases (GHG) emissions are significantly reduced thanks to the low GWP value of HCs. For example, in a typical supermarket, between 5 and 10% of the total local refrigerant is released into the atmosphere - using HCs as a substitute refrigerant reduces gas emissions by many tonnes per year.
On the other hand, the physical properties of HC-based systems - lower liquefaction point, thermodynamic advantages and higher coefficient of performance (COP) - combine to make energy efficient operation possible. For example, in an air conditioning system, using propane (R290) as a replacement for HFC-134a results in at least 80% reduction in greenhouse gas emissions.
Further advantages of HCs are the low-cost availability as a by-product in the extraction and processing of oil and gas as well as the fact that the achievable energy savings by HC systems has already been proven in many studies. Against this backdrop, hydrocarbons have long been proven to be a viable substitute for fluorocarbons and other environmentally harmful refrigerants.
Hydrocarbon Technologies
The importance of HCs has so far been most apparent in household and freezer units, where the Isobutane (R600a) refrigerant, which was first used in the Greenfreeze refrigerator for the first time, is now in use worldwide. In commercial refrigeration systems it is now the same, in supermarkets and many other places mainly propane (R290) is used as a replacement for the ozone depleting refrigerant. It is similar in the field of air conditioning. There you will find HCs in residential and office buildings. In addition, certain groundwater heat pumps use energy-saving propane (R290).
HC systems use the same cooling circuit as those with synthetic refrigerants. Propane (R290) is as refrigerant compatible with the equipment and equipment designed for the traditional - the ozone depleting - synthetic refrigerant R22; therefore, it is a direct replacement that is far superior in terms of performance to its synthetic competitor.
In summary, the HC technology has the following advantages:
- no destructive effect on the ozone layer
- significantly lower emissions of greenhouse gases
- low global warming potential and thus smaller contribution to global warming
- higher energy efficiency
- easy use
- Changeover with very low investment
Safety requirements
HCs are subject to international safety guidelines and laws because of their fire hazard. Their use is limited to a capacity of 150g per system, but exceeding this value in Europe is officially permitted under certain favorable conditions. All manufacturers of HC systems must adhere to safety rules, and their service personnel must understand and apply the prescribed procedures for the safe handling of HC. Government safety regulations demand leakage simulation tests and strict regulations apply to the insulation of electrical components in the vicinity of refrigerant flows. In addition, many domestic and commercial appliances, such as domestic refrigerators, freezers, heat pumps, commercial refrigeration and compressors, are subject to international safety regulations.
Market Overview
Isobutane (R600a) refrigeration systems today dominate the domestic refrigeration and freezer markets entirely in the European single market, 50% in China and good sales figures throughout the first world. Propane (R290) and other hydrocarbons are well established in commercial refrigeration and similar developments are already underway in air conditioning. An important future market is the USA. The influence of world brands such as McDonalds is not yet in sight. When HC systems establish themselves here, there is a great need for the necessary components.
Flammable refrigerant R600a and R290
R600a and R290 are hydrocarbons. These refrigerants are flammable and are only permitted for use in equipment that meets the requirements specified in the current revision of EN / IEC 60335-2-24. (To cover potential risks arising from the use of flammable refrigerants).
Consequently, R600a and R290 are the only refrigerants that can be used in household appliances because they meet the above standards. R600a and R290 are heavier than air and the concentration on the ground is always highest. R600a may only be stored and transported in approved containers and must be handled according to valid guidelines.
To perform service and repairs on R600a and R290 systems, service personnel must be trained accurately and properly.
This includes knowledge of tools, transport of the compressor and refrigerant as well as the relevant regulations and safety precautions.
No open fire when working with refrigerant R600a and R290!
Conversion of refrigerant R12 or R134a R600a is not allowed as the refrigerators are not approved for use with flammable refrigerant and electrical safety has not been tested to existing standards. The same applies to conversions of refrigerant R22, R502 or R134a R290. Secop compressors for flammable refrigerants R600a and R290 are equipped with a yellow warning label.
Typical applications
Household refrigerators and freezers
- bottle cooler
- Ice machines and refrigerated counters
- Commercial refrigeration equipment
- beer cooler
- Soda Fountain
- Dehumidifiers
- Heat pumps
R600a as replacement of R134a in household refrigerators
In 1993, the Greenfreeze refrigerator was introduced, which was developed by Greenpeace in collaboration with the East German manufacturer Foron (formerly VEB dkk Scharfenstein). It could be proved that R600a, although flammable, does not cause problems in a household refrigerator.
Greenpeace's campaign has put so much pressure on traditional manufacturers (Bosch-Siemens, Liebherr, Miele, AEG, Electrolux, Bauknecht) that they have decided to speed up the launch of R600a and phase out the recently launched R134a!
Also in 1993, Danfoss Compressors (Secop) introduced compressors for R600a.
Today, more than 700 million R600a domestic refrigerators are used worldwide.
By 2020, 75% of global production will be based on R600a.
"With kind permission of Secop GmbH"
Properties of Ammonia
Ammonia is toxic. It is a pungent gas that affects the respiratory organs and mucous membranes.
Ammonia is flammable. The ignition limit is 630°C, in the absence of catalytic steel even 850°C.
Ammonia cannot be ignited with a burning shaving, but it can be ignited with a welding torch.
Ammonia is explosive. The lower explosion limit in connection with air is 15.0%, the upper explosion limit is 30.2% (related to 20°C and 1.013 bar).
Why has such a dangerous substance been used as a refrigerant for 120 years?
- The manufacturing costs are low.
- The thermodynamic properties are favorable compared to other refrigerants.
- The ecological values are fine: ODP = 0, GWP = 0.
- Perceptions at 5 -10 ppm (volume in air)
ppm - parts per million - the millionth part of a unit
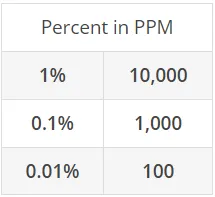
Usable Materials
The main material used is steel and its alloys. Galvanic surfaces are destroyed by ammonia.
Zinc is completely dissolved by ammonia in the presence of water.
Copper cannot be used as a material. Ammonium hydroxide forms in the presence of water. This readily dissolves copper to form the characteristic blue-colored copper-ammonium complex.
Phosphor bronze is the most resistant to ammonia. It is used in shaft seals. Alternative material is carbon and silicon carbide.
Mercury forms explosive mixtures with ammonia, and the addition of bismuth amalgam can help.
What are the concentration limits?
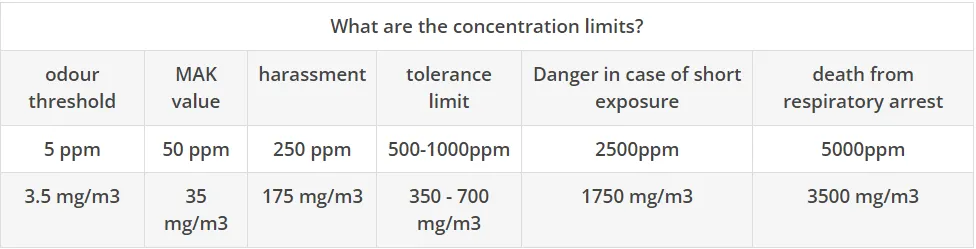
- MAK value 50 ppm
- 300 ppm hardly tolerable. Still harmless if exposed for more than an hour.
- 700 - 1,000 ppm unbearable. Prolonged exposure will damage the respiratory tract.
- 2,000 - 3,000 ppm fatal after 0.5 - 1 hour. Corneal inflammation occurs in the eyes.
- 5,000 - 6,000 ppm leads to blindness and death after 30 minutes
In the early 1980s, the international debate on the elimination of HCFCs and CFC refrigerants began, and with it the search for alternatives. It was decided to gradually reduce the use of these refrigerants by 2040 and then ban them altogether.
R22 was explicitly part of this solution. In the US, the use of R22 even increased thereafter, as the agreed goals were generally seen as unrealistic and it was believed that developing countries needed more time for a total phasing out of CFCs.
In the meantime, a global change of mind has begun, and accordingly, the 19th Conference of the Parties to the Montreal Protocol in September 2007 set stricter rules for phase-out periods:
Industrialized countries or non-Article 5 states:
Reduction of production and use of HCFCs (R22) by 75% by 2010 and by 90% by 2015; CFC ban from 2020.
Developing countries according to Article 5:
Reduction of production and use of HCFCs (R22) by 1% by 2010, by 35% by early 2020 and by 67.5% by 2025. Complete phase-out 2030. 2.5% of original CFCs Quantity are still allowed until 2040.
The accelerated phasing out of CFC over the next ten years means that it will no longer be possible to operate new plants with CFCs in both industrialized and developing countries .
In the United States, the Environmental Protection Agency (EPA) has established specific provisions to implement the Montreal Protocol, which aims to phase out R22 use by 2010. However, devices manufactured before 2010 can continue to operate until 2020.
To achieve this goal, several initiatives have been launched, including the EPC's GreenChill Advanced Refrigeration Partnership. It involves companies in the food industry as well as refrigeration equipment and refrigerant manufacturers. The partnership aims to help supermarkets withdraw R22. Currently, it is still used in more than 70% of US supermarkets. HFCs are clearly favored as an alternative in the US, as will be seen, for example, at the opening of the world's largest production facility for R32 in September 2007. The plant in Colvert City, Kentucky produces 25,000 tons of R32 per year. R32 is a component of HFC refrigerant blends such as R410A.
The new provisions have no impact on European legislation. The deadline for the complete ban on R22 in existing facilities is 31.12.2014. Use in new cooling, air conditioning or heat pump systems has been prohibited since January 2001. The use in combined air conditioning and heat pump systems since January 2004 prohibited.
Copyright Danfoss A / S (RA Marketing / MWA) June 2009
The refrigerant R1234ze(E) is a low flammable refrigerant and has a global warming potential ( GWP ) of less than 1. R1234ze(E) is an HFO (hydrofluoroolefin) refrigerant.
It is suitable for operation in chillers / chillers and heat pumps for commercial and industrial plants with positive displacement compressors and direct evaporation. It is classified according to ISO / ASHRAE in the safety class A2L (hardly flammable) and therefore allows significantly higher quantities than other flammable refrigerants.
With its GWP value of less than 1, R1234ze(E) falls below the limit of 150 set out in the F-Gas Regulation 517/2014 and the Ecodesign Directive. It is therefore not within the limits of the F-gas Regulation . Down scenario, because this refrigerant does not include any CO2 equivalents on the quantity of refrigerants placed on the market. R1234ze (E) is a low-flammability class 2L refrigerant. The permitted capacities, system configurations and guidelines for safe handling for the respective applications can be found in the applicable regulations and standards for your region, eg. PED, EN 378 or ISO 5149.
Applications for HFO refrigerants
R1234ze(E) is used inter alia as a basic component in HFO / HFKW blends. These blends have been developed as "Low GWP" alternatives to R404A / R507, R22 / R407C and R410A to meet regulatory requirements for reducing F-Gas-emissions (EU-F-Gases Regulation). Some of these refrigerants have already been tested in terms of refrigeration capacity and efficiency as part of AHRI's Alternative Refrigerants Evaluation Program (AREP) and also used in test facilities.
From the group of hydro-fluoro-olefins is another substance with the name R1234ze(E) is available, which has been used mainly as a blowing agent for PU foam and aerosol. R1234ze(E) differs from R1234yf by a different molecular structure. The thermodynamic properties also provide favorable conditions for use as a refrigerant. The global warming potential
is also very low (GWP100 = 7).
There is some uncertainty about flammability. In safety data sheets, R1234ze(E) is declared non-flammable. However, this only applies to transport and storage. When used as a refrigerant, there is a higher reference temperature for flammability tests of 60 °C. At this temperature, R1234ze(E) is flammable and therefore classified as R1234yf in safety group A2L.
R1234ze(E) is sometimes referred to as R134a substitute but is more than 20% lower in volumetric refrigeration capacity than R134a or R1234yf. The boiling point (-18 °C) also limits the application at lower evaporation temperatures strong. With positive displacement compressors, therefore, the preferred use is in high temperature applications.
application areas
- Air conditioning
- Heat pumps
- Commercial refrigeration
- Chillers
- industrial air conditioning
refrigeration plant
- Direct expansion
- new plants
Technical specifications
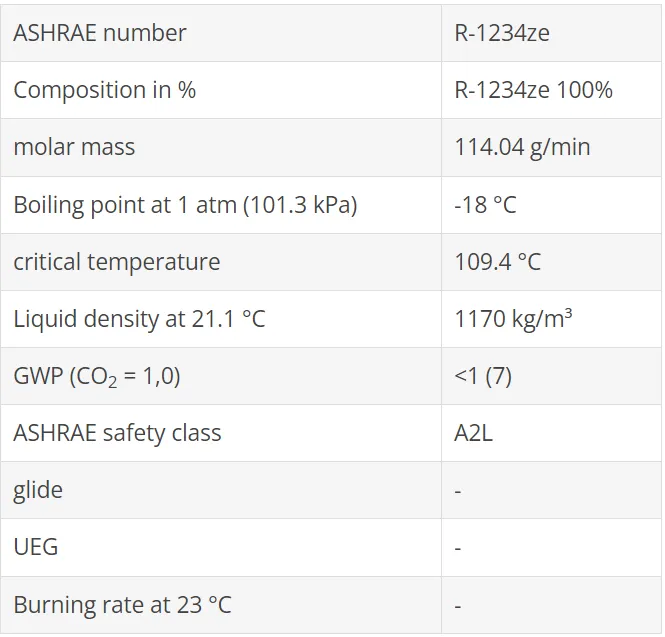